- Change theme
Maintenance Management: A Smarter Way to Handle Repairs and Upkeep
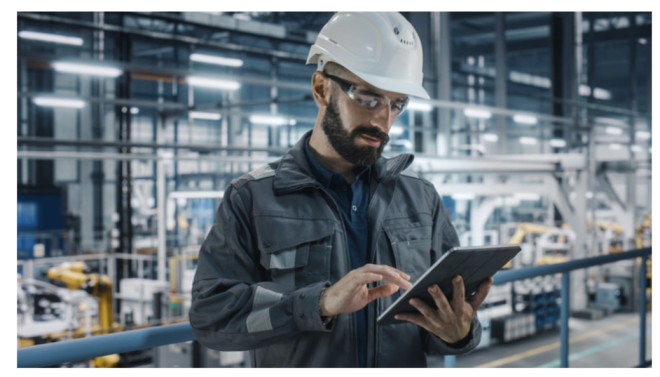
Maintenance management is essential for keeping equipment in top shape, yet many businesses still rely on outdated methods.
04:31 15 November 2024
Maintenance management is essential for keeping equipment in top shape, yet many businesses still rely on outdated methods. In fact, 44% of plants report spending over 40 hours a week on maintenance tasks. Timly’s digital maintenance management solution streamlines these processes by centralizing data and automating key tasks like scheduling and tracking repairs.
Whether your focus is on preventive maintenance or improving daily workflows, Timly helps reduce downtime and ensures your assets are always ready to perform.
The Role of Maintenance Management in Ensuring Compliance and Efficiency
Operational efficiency relies heavily on the consistent performance of equipment, especially in industries like metalworking where machinery faces complex demands.
Adhering to maintenance guidelines and safety regulations, such as those outlined by the UK Health and Safety Executive (HSE) and the Provision and Use of Work Equipment Regulations (PUWER), is essential. Regular inspections, like PAT testing, must be prioritized to avoid costly downtime.
Proper maintenance management not only extends the lifespan of machinery but also helps maintain its value. While some maintenance tasks, such as daily cleaning and inspections, can be handled by operators, more complex repairs may require specialists.
Timly’s maintenance management software simplifies these processes by providing a centralized system to schedule and track all maintenance tasks. Each asset is digitally recorded, with real-time updates on its status and upcoming maintenance requirements. Features like a mobile app and QR codes ensure that employees can easily access essential information, keeping them informed and on top of their maintenance responsibilities.
Why Excel Falls Short for Maintenance Management
While Excel is a familiar tool in most workplaces, it has some limitations when it comes to managing maintenance tasks. A digital maintenance management solution, like Timly’s asset management software, offers far more advanced features, streamlining workflows and boosting efficiency.
Timly’s cloud-based platform ensures that both office staff and production teams have real-time access to the latest information. With a built-in calendar view, scheduling maintenance becomes a breeze, and optional email reminders or notifications help ensure no task is overlooked.
One of the biggest advantages of Timly’s solution is its multi-user capability. Employees can access the system from their office computers or mobile devices on the shop floor, something Excel struggles to support efficiently. Managing large datasets on mobile devices through spreadsheets is cumbersome, but with a dedicated maintenance app, employees can easily incorporate maintenance tasks into their daily routines. This user-friendly approach increases adoption rates and reduces the risk of skipped or delayed maintenance activities.
Maintenance Planner App – An Essential Tool for Maintenance Management
Timly’s maintenance planner app is an indispensable tool for integrating maintenance management into your team's daily workflows. Since most employees already have access to a smartphone—either personal or company-issued—they can easily use the app with just an internet connection. By scanning a QR code attached to any machine, employees instantly gain access to detailed maintenance logs, instructions, and equipment history.
The app goes beyond just viewing data. Employees can document completed maintenance tasks, perform inspections, and report defects directly within the system. When necessary, the app can even generate repair orders automatically, streamlining the process for both internal teams and external service providers. This ensures that maintenance tasks are handled efficiently and with minimal disruption to operations.
Maintenance and Repair – Practical Use of Maintenance Management Software
Building a ‘smart workshop’ requires efficient tracking of equipment inventory, condition, and location. Timly’s maintenance management software simplifies this by monitoring every asset throughout its lifecycle.
Each item is tagged with a QR code, linking to a flexible profile that stores essential details—whether it’s a static asset like office furniture or complex machinery requiring detailed maintenance logs and repair documentation.
The software’s granular permission system ensures that employees only see the information relevant to their roles, enhancing security and focus. Additionally, Timly allows for the assignment of personal responsibility for equipment, creating greater accountability in workplaces where tools and machines are frequently shared. The app even makes it simple to transfer responsibility between team members when needed.
In high-risk environments like metalworking, where machinery such as CNC milling machines can pose safety hazards, compliance with safety protocols is essential. Timly’s system streamlines access to safety checklists, ensuring employees complete necessary inspections before or after repairs. This approach replaces outdated manual processes, helping you to meet occupational safety standards.
Maintenance Management Software in Metalworking
In industries like toolmaking and machining, where specialized machinery comes with high costs, thorough planning is essential. Maintenance management software helps your business address critical questions:
- When will repairs be needed?
- Will expensive replacement parts be required?
- How long will components last?
- Is the machine still cost-effective when considering operational expenses?
Timly’s software compiles this data into detailed digital files, empowering you to make informed, cost-saving decisions.
By leveraging comprehensive maintenance data, your business can predict breakdowns and associated costs more accurately. For instance, analyzing repair histories across similar machines allows businesses to anticipate future maintenance needs and budget accordingly. This proactive approach helps identify and mitigate cost drivers before they escalate.
Timly simplifies this process by centralizing all maintenance information. With built-in filtering tools, managers can quickly analyze maintenance data without sifting through multiple sources, ensuring they have the insights needed to keep operations running smoothly and efficiently.