- Change theme
How Convex Phased Array Transducers Improve Accuracy in Inspection of Thick Materials
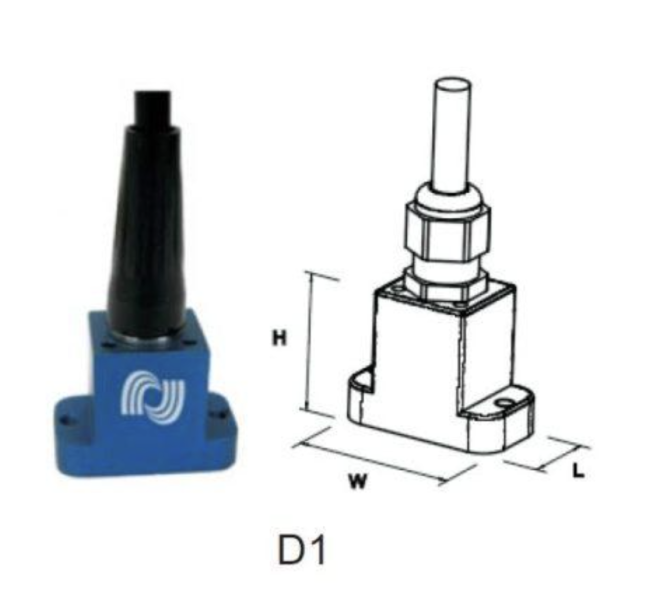
When dealing with thick materials like steel plates, pipelines, or pressure vessels, accurate and reliable inspection becomes a critical task.
17:52 20 March 2025
When dealing with thick materials like steel plates, pipelines, or pressure vessels, accurate and reliable inspection becomes a critical task. You need to ensure these materials are free of hidden flaws to maintain the integrity of your equipment. This is where the convex phased array transducer (CPAT) comes in, offering significant improvements in the way thick materials are inspected. In this article, we’ll explore how CPAT works, its benefits for thick material inspection, and why it’s becoming a preferred choice in industries like aerospace, oil and gas, and power generation.
What Makes Convex Phased Array Transducers Ideal for Thick Material Inspection?
Understanding Phased Array Technology
Phased array technology allows ultrasound beams to be electronically steered, focused, and shaped. This means the transducer can direct the sound waves in various directions, enabling it to scan deeper and more complex areas of the material. The key advantage of phased array transducers is their ability to adjust the beam in real-time, making them versatile and effective for a range of inspections.
The Advantage of Convex Shape for Thick Materials
Convex phased array transducers have several key benefits, especially when inspecting thick or curved materials:
- Wider Coverage: The convex shape allows for a broader scanning area, making it ideal for inspecting large components.
- Better Contact with Curved Surfaces: The convex design improves the probe's contact with curved or irregular surfaces, ensuring more accurate readings.
- Efficient Scanning: Unlike traditional flat probes, the convex shape provides more efficient scanning, which leads to better detection of internal flaws in thicker materials.
- Deeper Penetration: The design allows for better penetration of sound waves into thick materials, making it easier to detect deeper flaws.
- Improved Flaw Detection: The convex shape enhances the ability to detect internal defects, ensuring that even complex flaws are identified.
Overcoming Traditional Inspection Challenges
Traditional inspection methods, such as single-element transducers or manual ultrasonic testing, can struggle with detecting internal flaws in thick materials. They often provide limited resolution and depth penetration. In contrast, convex phased array transducers, such as those from NDT-KITS, can detect deeper and more complex internal flaws with much greater accuracy. This makes them more reliable for critical applications where hidden defects could lead to failure or safety risks.
Benefits of CPAT in Deep Defect Detection
Improved Focus and Depth Penetration
One of the main advantages of CPAT is its advanced focusing capabilities, which allow the ultrasound beam to penetrate thicker materials more effectively. This means you can detect deep-seated flaws such as cracks, voids, and inclusions that are often missed by traditional inspection methods. Whether you're inspecting thick steel plates or pressure vessels, CPAT provides the depth penetration needed for a comprehensive inspection.
Enhanced Sensitivity and Resolution
CPAT offers higher sensitivity and better resolution compared to conventional methods. This means it can detect even the smallest defects, which is crucial when inspecting materials used in high-risk industries like aerospace or power generation. With CPAT, you’re able to spot subtle defects like microcracks or small inclusions, which could otherwise go unnoticed, leading to costly repairs or safety concerns.
Higher Signal-to-Noise Ratio
Another key benefit of CPAT is its higher signal-to-noise ratio. Phased array technology ensures that the signal is strong enough to differentiate between actual defects and background noise, improving the accuracy of the results. This is especially important when inspecting thick materials, where background noise can often obscure potential flaws.
Real-World Applications of CPAT
Aerospace Industry
In the aerospace industry, safety is of utmost importance. CPAT is used to inspect thick structural components, such as engine casings or fuselage parts. By providing a more accurate and efficient way to detect internal flaws, CPAT helps ensure the safety and performance of critical aircraft components, preventing costly failures and enhancing overall reliability.
Oil & Gas Industry
The oil and gas industry relies on CPAT to inspect pipelines, pressure vessels, and other critical infrastructure. CPAT can detect issues like corrosion, cracks, or fatigue that could lead to accidents or environmental hazards. With the ability to detect defects deep within the material, CPAT helps maintain the integrity of oil rigs, pipelines, and refineries, reducing the risk of catastrophic failures.
Power Generation
In the power generation sector, CPAT is instrumental in inspecting thick-walled pressure vessels and steam pipes. These components need to be regularly inspected for internal flaws to ensure their safe operation. CPAT’s high sensitivity and depth penetration make it ideal for detecting flaws in these critical parts, helping to prevent costly shutdowns and ensuring continuous power generation.
Enhancing Inspection Efficiency with CPAT
Faster Inspections and Increased Coverage
CPAT significantly reduces inspection times. The wide coverage of convex phased array transducers allows you to inspect large areas in a single pass, reducing the overall time needed for inspections. This is particularly beneficial for industries where equipment downtime needs to be minimized. With faster inspections, you can increase productivity and reduce operational delays.
Real-Time Data for Immediate Decisions
CPAT provides real-time data and imaging, allowing you to make quick, informed decisions about the material's integrity. This real-time feedback is essential in environments where time-sensitive decisions are necessary, such as in manufacturing or emergency maintenance. You can immediately assess the results and take corrective actions if needed, enhancing operational efficiency.
Reduced Need for Multiple Inspections
With CPAT’s ability to scan large volumes of material and detect multiple defects in one pass, the need for multiple inspection methods or follow-up inspections is reduced. This makes the inspection process more streamlined and cost-effective, ultimately improving overall inspection efficiency.
Conclusion
Convex phased array transducers represent a significant advancement in the inspection of thick materials. By offering superior depth penetration, higher resolution, and real-time data, CPAT helps industries like aerospace, oil and gas, and power generation detect internal flaws more accurately and efficiently. Whether you are inspecting a pipeline or a pressure vessel, CPAT enhances inspection reliability and reduces downtime, making it an indispensable tool in maintaining the safety and integrity of your critical infrastructure.