- Change theme
An Overview of PCB Manufacturing Types and Techniques
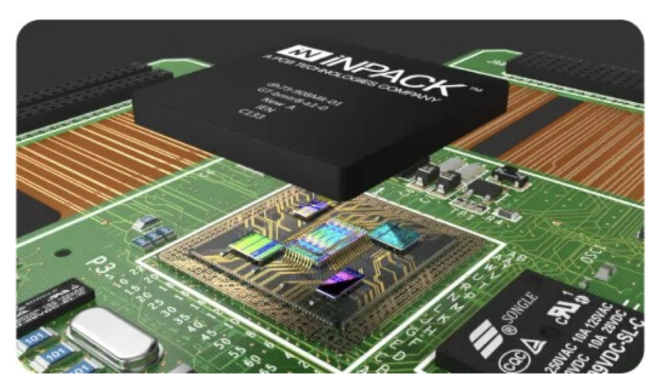
Printed Circuit Boards are the backbone of modern electronics, providing the necessary connections and support for electronic components to function.
05:05 16 January 2025
Printed Circuit Boards (PCBs) are the backbone of modern electronics, providing the necessary connections and support for electronic components to function. As technology advances and devices become more compact, the demand for high-quality, reliable, and efficient PCBs has grown significantly. PCB Manufacturers offer a variety of techniques (such as “wire bonding”) to cater to the increasingly sophisticated requirements of industries such as consumer electronics, automotive, telecommunications, and medical devices. This article provides an overview of the different types of PCB manufacturing and the techniques used to create them.
Types of PCBs
There are several types of PCBs, each designed to serve specific purposes and applications. The primary categories include single-sided, double-sided, multilayer, flexible, rigid-flex, and high-frequency PCBs. Let’s explore each in more detail:
- Single-Sided PCBs Single-sided PCBs are the simplest and most common type, typically used for basic electronic devices. These boards have a single layer of conductive material (usually copper) on one side, while the other side is used for components. Single-sided PCBs are ideal for low-density applications, such as household appliances, toys, and simple consumer electronics. They are cost-effective and easy to manufacture due to their straightforward design.
- Double-Sided PCBs Double-sided PCBs are similar to single-sided boards, but they have copper layers on both sides, allowing for more complex circuitry. These boards are often used in more advanced applications where a greater number of components need to be placed in a smaller space. Double-sided PCBs can be found in devices like power supplies, audio equipment, and computer peripherals. They provide more design flexibility but also require more careful consideration during the manufacturing process, especially in terms of component placement and vias (holes that connect the two sides of the board).
- Multilayer PCBs Multilayer PCBs consist of three or more layers of conductive material, stacked on top of each other and separated by insulating layers. These boards are used for high-density and high-performance applications, such as smartphones, computers, and communication systems. The multiple layers allow for more complex circuitry, better signal routing, and improved performance. While they offer substantial benefits in terms of functionality, multilayer PCBs are more expensive to manufacture due to the increased complexity and additional steps in the fabrication process.
- Flexible PCBs Flexible PCBs, also known as flex circuits, are designed to bend or fold without losing functionality. These boards are typically made from flexible materials like polyimide, allowing them to be shaped to fit into tight spaces or conform to unusual shapes. Flexible PCBs are often used in wearable electronics, medical devices, automotive applications, and aerospace equipment, where compactness and flexibility are essential. The manufacturing process for flexible PCBs is similar to traditional rigid boards but requires special attention to material handling and component placement.
- Rigid-Flex PCBs Rigid-flex PCBs combine the best of both rigid and flexible designs. These boards feature both rigid sections and flexible areas, allowing for compact and robust designs that can still bend or twist as needed. Rigid-flex PCBs are ideal for complex applications that require a combination of rigid board performance with the flexibility to fit in tight spaces. They are commonly found in applications such as cameras, medical devices, and military equipment. The manufacturing process for rigid-flex PCBs is more complex, as it requires precise assembly of both rigid and flexible layers, making them more expensive to produce.
- High-Frequency PCBs High-frequency PCBs are designed for applications that require high-speed signal transmission, such as radar systems, wireless communication devices, and high-end computing equipment. These boards are made from specialized materials, such as PTFE (polytetrafluoroethylene) or ceramics, which minimize signal loss and ensure reliable performance at high frequencies. The manufacturing process for high-frequency PCBs involves additional steps to ensure that signal integrity is maintained throughout the board.
PCB Manufacturing Techniques
The process of manufacturing a PCB involves several key stages, each requiring specialized techniques to ensure the final product meets performance and quality standards. Some of the most common PCB manufacturing techniques include:
- PCB Design and Layout The first step in PCB manufacturing is designing the layout of the circuit. This involves creating a schematic diagram of the components and their connections, followed by designing the physical layout of the PCB. PCB design software such as Altium Designer, Eagle, and KiCAD are commonly used to create these layouts. The design is critical as it dictates how well the PCB will function once manufactured, as well as its overall size and shape.
- Printing the PCB Design Once the design is complete, the next step is to transfer the design onto the PCB material. This is typically done using a process called photolithography, where a light-sensitive film is applied to the copper-clad board. The design is then exposed to ultraviolet (UV) light, hardening the areas of the film that correspond to the circuit pattern. The unexposed areas are washed away, leaving a pattern that matches the desired circuit.
- Etching After the PCB design has been printed onto the copper-clad board, the next step is etching. This process involves using a chemical solution to remove unwanted copper from the board, leaving behind only the copper traces that form the circuit. Etching is typically done using a mixture of copper chloride or ferric chloride. The result is a precisely etched circuit pattern that will connect the components.
- Drilling After the etching process, the PCB must be drilled to create vias (holes that allow electrical connections between different layers of the board) and holes for component leads. Drilling is typically done using a computer-controlled drill press or laser to ensure precision. The quality of drilling is essential for ensuring reliable connections and the overall functionality of the PCB.
- Plating and Coating Once drilling is complete, the PCB undergoes a plating process. In this step, a thin layer of metal, usually copper, is plated onto the drilled holes and the exposed copper traces. This ensures that the vias are conductive and properly connected to other parts of the board. Additionally, the PCB is coated with a protective layer, typically made of solder mask, which helps protect the traces and prevents short circuits.
- Component Placement and Soldering The final step in PCB manufacturing involves placing and soldering the electronic components onto the board. In automated PCB assembly (PCBA), machines are used to pick and place components onto the board, followed by reflow soldering or wave soldering to create strong electrical connections. Manual soldering may be used for certain delicate components or in small-scale production.
- Testing and Quality Control After the components are soldered onto the board, it undergoes a series of tests to ensure that it meets the required specifications. These tests include electrical testing, visual inspections, and functional testing to verify that the PCB operates correctly. Testing ensures that the final product is free of defects and will perform reliably in its intended application.
PCB manufacturing is a multi-step process that involves various techniques to ensure the high-quality production of printed circuit boards. From single-sided to multilayer, flexible to rigid-flex, each type of PCB is suited for specific applications, with its own unique set of advantages and manufacturing challenges. Understanding the different PCB manufacturing techniques—such as photolithography, etching, drilling, plating, and component placement—is essential for creating reliable, functional boards. As technology continues to evolve, PCB manufacturing techniques will also advance, enabling the creation of smaller, faster, and more efficient electronic devices.