- Change theme
A Look into Growing Demand and How to Get an Injection Mold Quotation
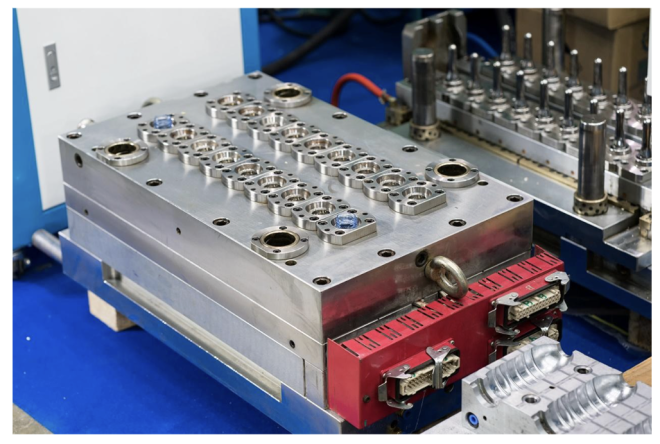
The global injection molding industry is experiencing robust growth, driven by increasing demand for plastic components across various sectors.
02:36 13 December 2024
The global injection molding industry is experiencing robust growth, driven by increasing demand for plastic components across various sectors, from automotive to medical devices. As industries continue to rely on the cost-efficiency and precision of injection molding, manufacturers and businesses alike are focusing on optimizing their production processes to meet rising customer needs. However, with the complexity of the injection molding process, companies must carefully consider design, material selection, and production methods, making the need for accurate injection mold quotations more important than ever.
The Surge in Demand for Injection Molding
Injection molding is a key manufacturing process in the production of plastic parts, used extensively in industries like automotive, consumer electronics, medical devices, and packaging. With its ability to produce high volumes of precise parts quickly and cost-effectively, the technology has become indispensable in meeting the demands of today’s fast-paced manufacturing environment.
The increasing focus on automation and smart manufacturing techniques has played a pivotal role in the growth of the injection molding market. In fact, industry analysts predict that the global injection molding market will continue to grow at a healthy pace over the next decade. This growth is attributed to factors such as rising demand for lightweight materials, particularly in automotive and aerospace, as well as the expanding use of injection molding in medical device production, which requires highly precise and reliable parts.
The Importance of an Injection Mold Quotation
When embarking on an injection molding project, one of the first steps a business must take is to obtain a detailed Injection Mold Quotation. An injection mold quotation is an essential document that provides a breakdown of the costs associated with creating a custom mold and producing parts through injection molding. This quotation is often the deciding factor in selecting a manufacturer, as it gives the company a clear understanding of production costs, lead times, and the overall investment required.
An accurate Injection Mold Quotation can help businesses plan their budgets and set realistic expectations for delivery times. It includes several key elements, such as:
- Tooling Costs: This covers the design, engineering, and construction of the injection mold itself. Tooling is one of the most significant upfront costs in injection molding and can vary depending on the complexity of the part design.
- Material Costs: Different plastics are used in injection molding, each with its unique cost profile. A detailed quotation will break down material costs based on the type of resin selected.
- Production Volume and Cost per Unit: The cost per part decreases significantly with larger production volumes. A proper quotation will factor in the expected number of units and provide a per-unit cost breakdown.
- Lead Time and Delivery: The time it takes to produce a mold and begin mass production is another crucial aspect covered in the quotation. Lead times can vary based on the complexity of the mold and the schedule of the manufacturer.
- Post-Production Services: In some cases, additional services such as finishing, assembly, or packaging may also be included in the quotation. These services can add value to the final product and may be necessary for businesses looking for a comprehensive manufacturing solution.
How to Get an Accurate Injection Mold Quotation
Obtaining an accurate injection mold quotation requires collaboration between the business and the manufacturer. The process usually begins with providing detailed design files, such as CAD drawings or 3D models of the parts to be molded. The manufacturer will then review these files and assess the complexity of the mold, as well as other factors like material selection, part size, and production volume.
Here’s a closer look at the steps involved in obtaining a reliable Injection Mold Quotation:
- Design Submission: Submit detailed designs and specifications for the parts you want to produce. The more precise and comprehensive the design, the more accurate the quotation will be.
- Material Selection: Decide on the type of plastic you want to use for your parts. Materials vary in cost, strength, and durability, so the choice of material will significantly affect the quotation.
- Quantity Estimates: Provide estimates of how many parts you need. Higher quantities typically lead to lower per-unit costs, but this depends on the efficiency of the production process and the complexity of the parts.
- Mold Complexity Assessment: The more intricate the mold, the more expensive and time-consuming the production process will be. Manufacturers will analyze the design for any features that may require additional engineering, such as inserts, undercuts, or complex geometries.
- Tooling and Production Cost Estimation: Based on the design, material, and mold complexity, the manufacturer will calculate tooling and production costs. Tooling costs are a significant upfront investment, while production costs will depend on the number of parts needed.
- Review of Lead Times: Depending on the manufacturer’s workload and the complexity of the project, lead times for mold production and part manufacturing can vary. Discussing and aligning expectations around lead times will help prevent delays and ensure timely delivery.
Challenges in the Injection Molding Process
While injection molding is a highly efficient and effective method for producing plastic components, it does come with its challenges. For businesses seeking to keep production costs low, the initial tooling cost can be a significant barrier. Molds can be expensive, especially for complex parts or those requiring special materials. However, for high-volume production, injection molding remains one of the most cost-effective methods, as the cost per part decreases significantly with larger quantities.
Another challenge is ensuring consistency and quality control across large production runs. Even slight changes in temperature, pressure, or cooling time can affect the quality of the molded parts. Manufacturers must maintain strict quality control measures to ensure that each part meets the required specifications. This is especially critical in industries like medical devices or automotive, where precision is non-negotiable.
Future Trends in Injection Molding
Looking ahead, the injection molding industry is expected to continue evolving, with several key trends shaping the future of the market:
- Sustainability: As demand for sustainable products increases, manufacturers are turning to eco-friendly materials, such as biodegradable plastics or recycled resins, to meet consumer demand for green products.
- Automation and Smart Manufacturing: The integration of robotics, AI, and machine learning is enhancing the efficiency and precision of injection molding. Automated systems are reducing human error, improving cycle times, and ensuring consistent product quality.
- 3D Printing and Hybrid Technologies: While traditional injection molding remains dominant, 3D printing is increasingly being used in combination with injection molding for rapid prototyping and low-volume production. This hybrid approach allows for more flexible production and faster time-to-market.
- Customization and On-Demand Manufacturing: With the rise of digital technologies, businesses are now able to offer more customized products without significantly increasing costs. This shift toward on-demand manufacturing allows companies to meet unique customer demands while keeping production costs low.
Conclusion
As industries continue to rely on the efficiency and versatility of injection molding, obtaining an accurate Injection Mold Quotation has never been more crucial. It provides a clear understanding of the costs, lead times, and production capabilities needed to bring a plastic component to life. By collaborating closely with experienced manufacturers, businesses can ensure that they get the best value from their injection molding projects—whether they are producing high volumes of consumer products, automotive parts, or precision medical devices. With the right design, material selection, and cost analysis, injection molding will remain a cornerstone of modern manufacturing for years to come.